Ceramic Fibers: A Comprehensive Guide to Their Properties and Applications
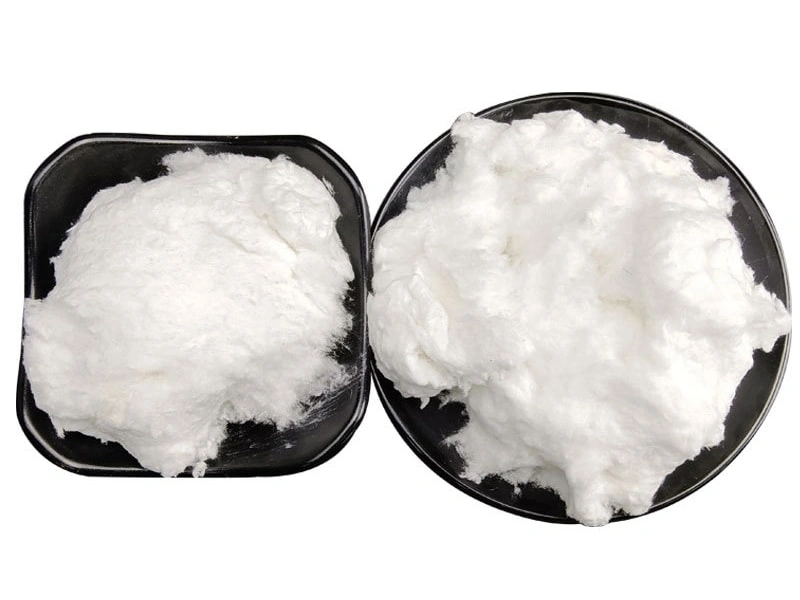
Introduction
Ceramic fibers are advanced materials known for their exceptional thermal, mechanical, and chemical properties. These fibers are widely used in industries that require materials capable of withstanding extreme temperatures, corrosive environments, and mechanical stress. This article provides an in-depth look at ceramic fibers, their types, properties, production methods, and application areas. By the end of this article, you will have a thorough understanding of why ceramic fibers are indispensable in modern industrial applications.
What are Ceramic Fibers?
Ceramic fibers are a type of high-performance material made from inorganic compounds, primarily aluminum oxide (Al₂O₃), silicon dioxide (SiO₂), and other metal oxides. These fibers are known for their high melting points, low thermal conductivity, and excellent resistance to thermal shock and chemical corrosion. They are typically used in applications that require insulation, structural reinforcement, and thermal management.
Key Properties of Ceramic Fibers
High Temperature Resistance: Ceramic fibers can withstand temperatures ranging from 1000°C to 1600°C (1832°F to 2912°F), making them suitable for high-temperature applications.
Low Thermal Conductivity: Their low thermal conductivity makes them excellent insulators, reducing heat loss and improving energy efficiency.
Chemical Stability: Ceramic fibers are resistant to most chemicals, including acids, alkalis, and solvents.
Mechanical Strength: They possess high tensile strength and rigidity, which are crucial for structural applications.
Lightweight: Despite their strength, ceramic fibers are relatively lightweight, which is beneficial for applications where weight is a concern.
Types of Ceramic Fibers
Ceramic fibers can be broadly categorized based on their composition and properties. The most common types include:
1. Alumina Fibers
Alumina fibers are composed primarily of aluminum oxide (Al₂O₃). They are known for their high temperature resistance, mechanical strength, and chemical stability. Alumina fibers are used in applications that require durability under extreme conditions, such as aerospace and automotive industries.
2. Silica Fibers
Silica fibers are made from silicon dioxide (SiO₂). They are known for their excellent thermal insulation properties and resistance to thermal shock. Silica fibers are commonly used in the production of insulation materials for industrial furnaces and kilns.
3. Aluminum Silicate Fibers
Aluminum silicate fibers are composed of a mixture of aluminum oxide (Al₂O₃) and silicon dioxide (SiO₂). They offer a balance of thermal stability, chemical resistance, and cost-effectiveness. Aluminum silicate fibers are widely used in the construction of industrial furnaces, kilns, and fireproof materials.
4. Zirconia Fibers
Zirconia fibers are made from zirconium dioxide (ZrO₂). They are known for their exceptional thermal stability and resistance to thermal shock. Zirconia fibers are used in applications that require materials to withstand extremely high temperatures, such as in the aerospace and nuclear industries.
5. Carbon Fibers
Carbon fibers are composed primarily of carbon atoms. They are known for their high strength-to-weight ratio, thermal conductivity, and electrical conductivity. Carbon fibers are used in a wide range of applications, including aerospace, automotive, and sports equipment.
Production Methods of Ceramic Fibers
The production of ceramic fibers involves several sophisticated techniques to ensure the material meets the required specifications for high-performance applications. The most common methods include:
1. Sol-Gel Process
The sol-gel process is a widely used method for producing ceramic fibers. It involves the following steps:
Preparation of the Sol: A colloidal suspension (sol) of ceramic precursors is prepared.
Gelation: The sol is then converted into a gel by controlling the pH and temperature.
Drying: The gel is dried to remove the liquid component, resulting in a porous structure.
Sintering: The dried gel is sintered at high temperatures to form the final ceramic fiber.
2. Melt Spinning
Melt spinning is another method used to produce ceramic fibers. This process involves:
Melting: The ceramic material is melted at high temperatures.
Spinning: The molten material is then spun into fibers using a spinneret.
Cooling: The fibers are rapidly cooled to solidify them.
3. Chemical Vapor Deposition (CVD)
CVD is a more advanced technique used to produce high-purity ceramic fibers. It involves:
Vaporization: Ceramic precursors are vaporized.
Deposition: The vapor is deposited onto a substrate, forming ceramic fibers.
Annealing: The fibers are annealed to improve their crystallinity and strength.
Application Areas of Ceramic Fibers
Ceramic fibers' unique properties make them suitable for a wide range of applications across various industries. Below are some of the key application areas:
1. Aerospace Industry
The aerospace industry demands materials that can withstand extreme temperatures and mechanical stress. Ceramic fibers are used in:
Thermal Protection Systems: Ceramic fibers are used in the thermal protection systems of spacecraft and re-entry vehicles to protect against the intense heat generated during re-entry.
Engine Components: They are used in the manufacturing of engine components that are exposed to high temperatures and corrosive environments.
2. Automotive Industry
In the automotive industry, ceramic fibers are used in:
Exhaust Systems: Ceramic fibers are used in the insulation of exhaust systems to reduce heat loss and improve fuel efficiency.
Brake Pads: They are used in the production of high-performance brake pads that require excellent thermal stability and wear resistance.
3. Energy Sector
The energy sector benefits from ceramic fibers in several ways:
Insulation in Power Plants: Ceramic fibers are used as insulation material in power plants to improve energy efficiency and reduce heat loss.
Nuclear Reactors: They are used in the insulation of nuclear reactors due to their high temperature resistance and chemical stability.
4. Industrial Furnaces
Ceramic fibers are widely used in industrial furnaces for:
Lining: They are used as a lining material in high-temperature furnaces to improve thermal efficiency and extend the lifespan of the furnace.
Kilns: Ceramic fibers are used in the construction of kilns for the production of ceramics, glass, and metals.
5. Chemical Processing
In chemical processing, ceramic fibers are used in:
Reactor Linings: They are used as a lining material in chemical reactors to protect against corrosive chemicals and high temperatures.
Filtration: Ceramic fibers are used in high-temperature filtration systems to remove impurities from gases and liquids.
6. Electronics
The electronics industry utilizes ceramic fibers in:
Substrates: They are used as a substrate material for electronic components that require high thermal stability and electrical insulation.
Heat Sinks: Ceramic fibers are used in the production of heat sinks to dissipate heat generated by electronic components.
7. Fire Protection
Ceramic fibers are used in fire protection applications due to their high temperature resistance and low thermal conductivity. They are used in:
Fireproof Clothing: Ceramic fibers are used in the production of fireproof clothing for firefighters and industrial workers.
Fire Barriers: They are used in the construction of fire barriers to prevent the spread of fire in buildings and industrial facilities.
8. Construction Industry
In the construction industry, ceramic fibers are used in:
Insulation Materials: They are used as insulation materials in buildings to improve energy efficiency and reduce heat loss.
Fireproofing: Ceramic fibers are used in the fireproofing of structural elements to enhance fire safety.
9. Medical Applications
Ceramic fibers are being explored for potential medical applications, such as in the development of biocompatible implants and drug delivery systems. Their chemical stability and biocompatibility make them a promising material for these applications.
Future Prospects and Innovations
The demand for high-performance materials like ceramic fibers is expected to grow in the coming years, driven by advancements in technology and the need for more efficient and durable materials. Some of the future prospects and innovations in the field of ceramic fibers include:
1. Nanotechnology
The integration of nanotechnology in the production of ceramic fibers is expected to enhance their properties further. Nanofibers with higher surface area and improved mechanical strength are being developed for specialized applications.
2. Composite Materials
Research is ongoing to develop composite materials that combine ceramic fibers with other high-performance fibers to create materials with superior properties. These composites could find applications in aerospace, automotive, and other industries.
3. Sustainable Production
Efforts are being made to develop more sustainable production methods for ceramic fibers, reducing the environmental impact of their manufacturing process. This includes the use of renewable energy sources and recycling of waste materials.
4. Medical Applications
Ceramic fibers are being explored for potential medical applications, such as in the development of biocompatible implants and drug delivery systems. Their chemical stability and biocompatibility make them a promising material for these applications.
Conclusion
Ceramic fibers are versatile and high-performance materials that have found applications in a wide range of industries, from aerospace to fire protection. Their exceptional thermal, mechanical, and chemical properties make them an ideal choice for demanding environments. As technology continues to advance, we can expect to see further innovations in the production and application of ceramic fibers, opening up new possibilities and expanding their use in various fields.
Whether it's in the construction of next-generation spacecraft or the development of sustainable energy solutions, ceramic fibers will undoubtedly play a crucial role in shaping the future of high-performance materials. By understanding the unique properties and applications of ceramic fibers, industries can make informed decisions about their use, ensuring that they leverage their full potential to achieve their goals. As research and development continue, the possibilities for ceramic fibers are virtually limitless, promising a future where these remarkable materials continue to drive innovation and progress across multiple sectors.